All You Need To Know About Flexo Printing
When it comes to the label printing industry, you will never fail to hear about flexo printing. This form of printing has grown and become one of the most commonly-used methods of printing labels. That is because it offers excellent productivity levels, unmatched flexibility, and high-quality results. As a result, more people are turning to this form of printing, and soon enough, it will take over the labels industry. So keep reading to learn more about Flexo printing and how it can help your business.
What is Flexo Printing?
Flexo or Flexographic printing is a unique printing technique that sees the use of a flexible printing plate. Initially, when this form of printing first came into use, the printing plates were made from rubber. However, modern flexographic printers have photopolymer printing plates. This and other developments have made it possible to mass-produce labels.
The main allure of flexo printing is that it adapts well to various materials. Additionally, it can use a wide range of inks. These presses can therefore print on paper, corrugated cardboard, films, foil and more. Additionally, they can use water-based inks and UV inks. Because of the versatility they offer, flexo printing presses are ideal for label printing.
How Does Flexo Printing Work?
The flexible photopolymer plate wraps around a rotating cylinder for each colour of the print. The graphics and text for each colour rise from the surface of the plate, similar to letterpress printing. Thus only the raised areas of the plate receive ink.
The standard press has four types of rollers, each with a specific function. First, the fountain roller will deliver ink from an ink pen to the steel or ceramic anilox roller and then to the plate cylinder.
These processes will apply the ink onto the substrate as the paper passes between the plate cylinder and a polished metal impression cylinder. This cylinder will apply the pressure needed to transfer the ink from the plate onto the substrate.
Additionally, the anilox roller’s primary function is to transfer a uniform thickness of ink to the flexible printing plate. This is thanks to the finely engraved cells on each roller that have a specific ink capacity. A doctor blade is often in place to scrape the anilox roller to ensure that only the ink on the engraved cells reaches the printing plate.
The substrate will move through the press, applying a different colour at each printing deck. Drying units (that use hot air or infrared or ultraviolet light depending on the ink) at every printing deck ensure that each colour dries completely.
Additionally, there are different forms of flexographic presses such as:
- Stack Press, where the printing decks are vertically positioned, allowing them to print both sides of the material as it moves through the printer.
- Central Impression (CI) Press, which sees the printing decks placed around a single large impression cylinder.
- In-Line Press features printing decks aligned in a straight line for easy handling of heavy substrates such as corrugated boxes.
As for inks, this form of printing can use different types of ink. The process can use energy-curable inks cured by UV light or electron beam (EB) systems. These inks are best for printing outer wraps for food packaging. The presses also use water-based inks. These are best for printing on corrugated packaging. Additionally, they use solvent-based inks, which are best for printing plastic shopping bags and industrial films.
Advantages of Flexo Printing
The main benefits of flexo printing are:
- It is fast. This form of printing is speedy. It runs at fast speeds. Therefore, it is best used for long runs. If you need label printing in a hurry, this is the ideal form of printing for you.
- It is flexible. This form of printing supports the use of different types of ink. Additionally, it can print on a variety of substrate materials. Whatever form of packaging you choose, this printing will come through effectively.
- It has excellent results. This form of printing produces superior results that do not need additional processes to make them stand out. It eliminates the need for varnishing or laminating to make the print look good. Instead, a single run produces excellent results that will last long.
- It requires little knowledge. This form of printing is pretty straightforward. It is easy to grasp, and so even less-trained operators can use it to achieve the desired output.
- It is low-maintenance. Lastly, these presses do not require a lot of maintenance, just basic routines, and they will keep functioning properly.
In conclusion, this form of printing is best for simple designs. Therefore, it is ideal for industries that require mass production of packaging materials for various items. With longer runs, you can expect lower prices. Additionally, you will enjoy the excellent quality results that they offer.
Also see Label Stickers Printing Nairobi, Packaging boxes.
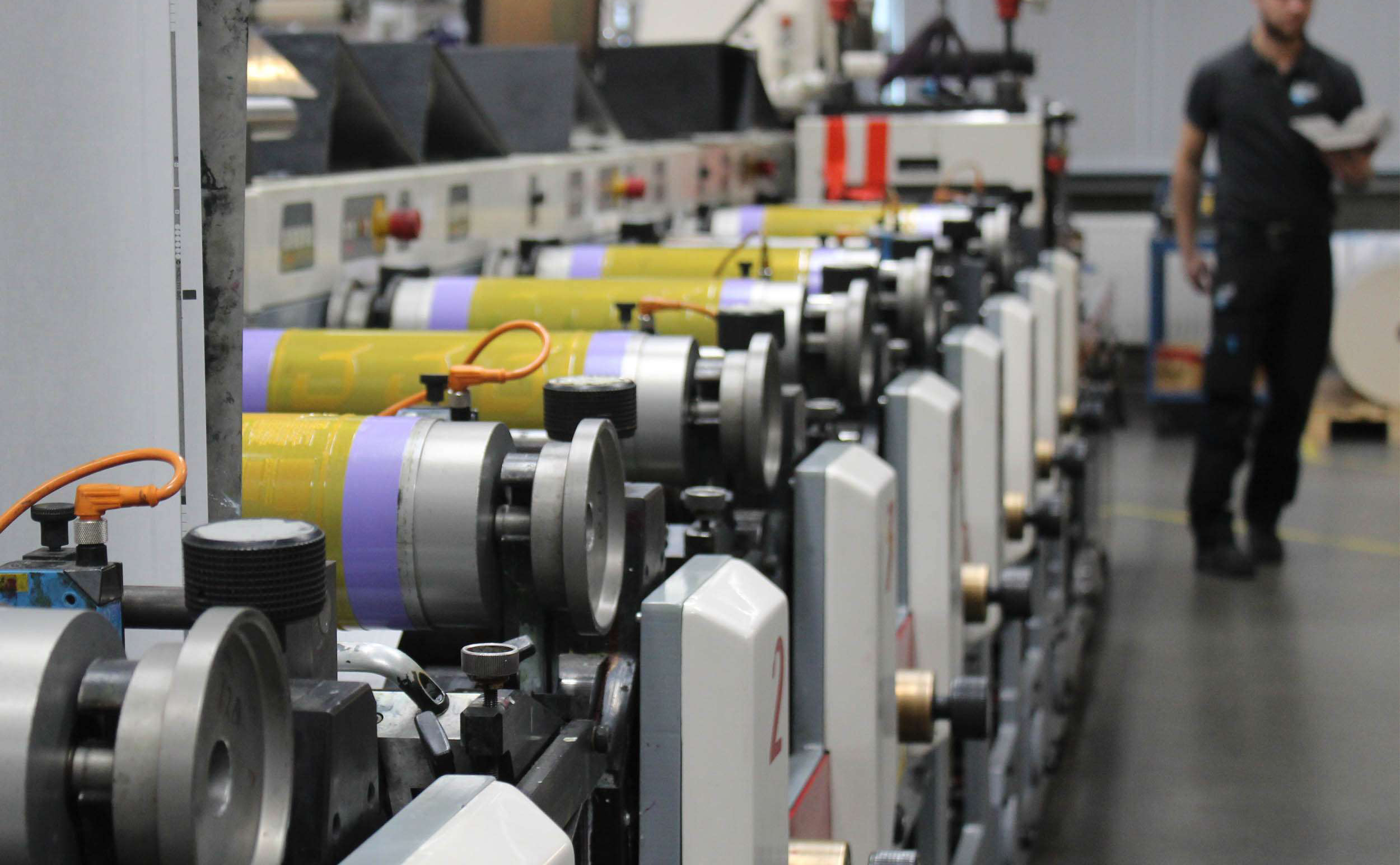